IAQ IQ Fall, 2017
©2017 Jeffrey C. May
As most of you know, I used to be a home inspector before I specialized in indoor air quality (IAQ). These two professions are not as distinct from one another as you might think; there is overlap in what home inspectors look for and do, and what I look for and do.
For example, I always inspect the exterior of a property first, to see if there are any visible conditions that might result in moisture intrusion.
Such conditions include window-cap flashings that are slanted toward rather than away from the cladding; signs of gutter splash at the perimeter of the house; and cracks in the pavement next to the foundation through which water can migrate toward the foundation wall. On the interior, I’m always concerned about the
condition of a duct system. In a house with hotair heat and/or central air conditioning, most of the air that occupants breathe is delivered through ducts. In a house with both hot-air heat and central air conditioning, people inhale the air from the ducts all year round.

What about panned bays? I wish they had never been invented, frankly, because they are difficult (if not sometimes impossible) to clean, and they are open to allergenic dust within the framing.
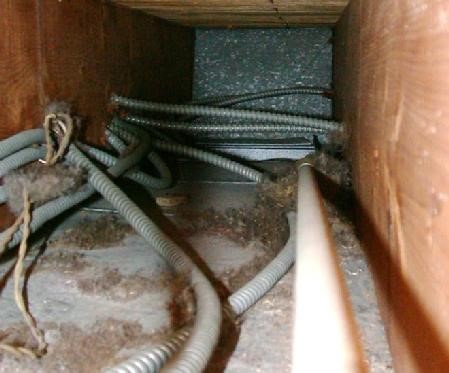
Don’t assume that ducts will be clean in new construction. An HVAC system is used at one time or another during construction or renovation work, and the ducts become contaminated with construction debris, including drywall dust and biodegradable sawdust.
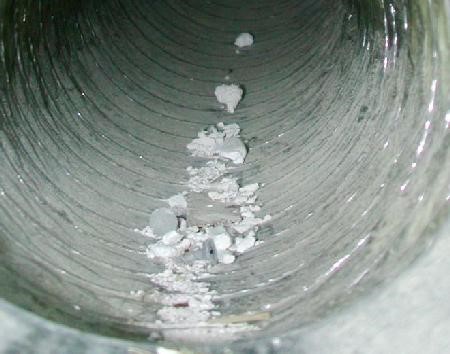
Unfortunately, flexible ducts can’t really be thoroughly cleaned and may have to be replaced if contaminated. And moldy duct board? Forget it!
I inspected one property that was still under construction. The metal duct sections were lying on the basement floor. It was winter, and workers were sawing wood in the basement, where surfaces were covered with biodegradable sawdust. Those surfaces included the ducts, unfortunately, so they were contaminated even before they were installed.
I hate to see fibrous lining material inside air handlers and ducts, because the material captures biodegradable dust. If you see condensation on metal ducts that have internal fibrous lining material, there’s a good chance
that there is mold growth within the ducts due to conditions of elevated relative humidity (metal is cold, the fibrous lining material in touch with metal is cooled, the material captures dust when filtration is inadequate, and mold takes root).
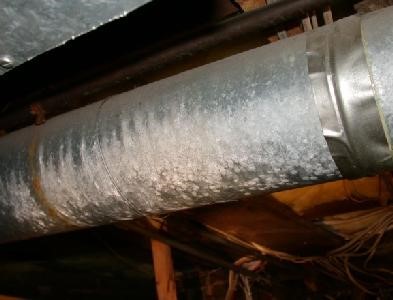
A leaking central humidifier can lead to mold growth within the return plenum.
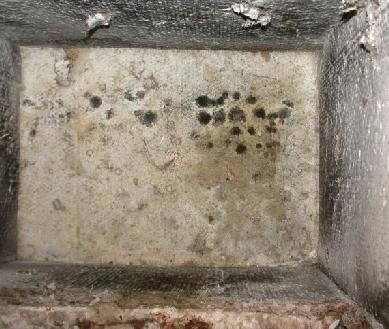
As we all know, air in a house rises from bottom to top and out, especially in the heating season. If a duct boot on the first floor is not flush to the flooring, and the basement or crawl space below is musty, airflows moving through the gaps can carry spores and musty odors from the belowgrade space up into the first floor.
I’ve found toys and cheerios, among other things, in boots. In one instance, I found a halfeaten donut and an empty cup of coffee in a duct.
In Massachusetts at least, home inspectors are not required to note environmental conditions. Still, I’d recommend that you look inside ducts
for any debris and signs of wetting. Explain to your Client how panned bays can be problematic. If it is readily accessible, open the blower access panel to see if there is internal fibrous lining material present, if the material contains dust, and even if the material already has spots of probable mold.
I will end with this story.
A couple that had just purchased the property hired me to do some indoor-air-quality sampling because they were experiencing allergy symptoms in the house. They weren’t worried about mold, they told me, because at their home inspector’s recommendation, they had hired him to include mold testing as part of his inspection.
He had taken a few air samples and sent them to a lab, which then sent the report to the couple. The report was reassuring, because very few mold spores were found in the samples.
Air samples alone do not identify the sources of indoor-air-quality contaminants, and if those sources have not been recently disturbed prior to the testing, the test results can be falsely reassuring.
Unfortunately, there was plenty of mold growth in the air handler in the basement, as well as in a carpet laid directly on concrete in the finished basement playroom. The couple was incensed and was considering legal action against the home inspector.
So while I am encouraging you to keep an eye out for visible conditions in a duct system that could lead to mold growth, I’m cautious about encouraging you to do mold testing yourself – particularly if you only take air samples.
That said, I still believe that home inspectors are the best people to learn about best practices for IAQ testing and investigations, because they have a thorough understanding of a building as a system. And such an understanding is of vital importance in the IAQ profession.
Indoor Air Quality professionals can learn a lot about buildings from home inspectors. Look on-line to find contact information for home inspectors in your area, and see if they will take you on a “ride-along” to some of their inspections. Go to www.homeinspector.org.
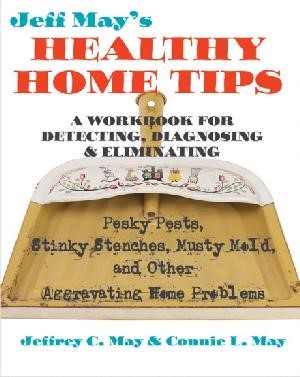
A good handbook for your clients.
Wish I got more than $.75/copy in royalties! Available on amazon.com.